ArcelorMittal Europe today announces the details of its CO2-free green steel strategy.
This will enable the company to offer its first environmentally friendly steel solutions to customers this year (30,000 tonnes), and expand this offer in the coming years (to 120,000 tonnes in 2021 and 600,000 tonnes by 2022) to meet its CO2 emissions target of 30 % by 2030 and reach zero by 2050.
The strategy is centered around two main technology routes, as presented in the first ArcelorMittal Europe Climate Action Report, published earlier this year:
• Use of hydrogen in DRI-EAF as well as blast furnace
• Expansion of the Smart Carbon route, which also uses hydrogen.
HYDROGEN
Hydrogen plays a central role in the company's decarbonization strategy. ArcelorMittal Europe is developing a series of industrial hydrogen projects for use in blast furnace steelmaking that will begin to deliver significant CO2 savings even over the next five years, and is also moving forward with a project to test hydrogen's ability to reduce iron ore and generate industrial-scale DRIs.
Ultimately, to reach zero, this hydrogen must be "green" (produced by electrolysis, which is powered by renewable electricity). Therefore, ArcelorMittal is developing new plants for the production of green hydrogen using electrolysers. ArcelorMittal teams in Bremen, Germany are working on the first large-scale implementation of this technology, which can then be applied both in the blast furnace and on the DRI-EAF route. Previously, this emerging technology was tested only in small pilot plants in Europe.
1. Hydrogen and blast furnace.
• ArcelorMittal Bremen
With the electrolyser installed, hydrogen can be produced and pumped in large volumes into the blast furnace tuyeres. The project will reduce the amount of coal required for the iron ore recovery process, thereby reducing CO2 emissions.
• IGAR in Dunkirk
At ArcelorMittal Dunkirk, the company is developing a hybrid blast furnace process that includes DRI gas injection into a blast furnace shaft as well as the use of blast furnace tuyere gas injection using plasma technology to create reducing gas. This is the first large-scale implementation of what is essentially a hybrid BF /DRI technology. Over time, this will allow green hydrogen to be introduced into the blast furnace as it arrives.
• Injection into a blast furnace at flat products sites
ArcelorMittal Europe is also implementing projects in almost all of its flat products plants to use gases from various sources for injection into blast furnaces. Coke oven injection
ArcelorMittal Europe will produce steel using hydrogen technology already in 2020
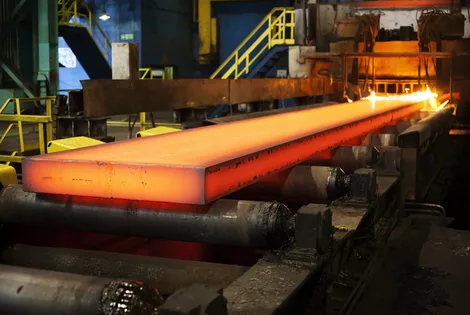
![]() |
Azovpromstal® 14 October 2020 г. 11:12 |